Nano-PVDF Aluminum Composite Panel, ACP Panel
Aluwedo® Nano PVDF aluminum composite panels adopt a new technology to change the molecular structure of paint surface. This techique improves and enhances the paint coating by giving it a longer color and gloss retention. It is applied as the 4th coating layer above the 3rd layer of PVDF coating. The 4th layer of Nano coating which is made from a water soluble chemical seals any air gaps between the tiny paint molecules thus preventing dirt, water, permanent paint or any particles trying to penetrate through the paint surface, making the paint surface lipophobic and hydrophobic.
Aluwedo Nano coating Aluminum composite panel (ACP) is designed to restore, enhance and extend the surface life of "freshly painted" or "oxidized" painted surfaces by 10 years. Some organizations have invested billions of dollars to protect the large-value assets destroyed from corrosion, scratching, chipping, chemical attack or weathering. Many of these assets were painted using inferior materials not designed to withstand long-term weathering and service.
We have various options when these painted assets degrade:
1. Do nothing and allow the paint weathering cycle to continue (resulting in decreased corrosion, chemical and UV resistance).
2. Replace the existing paint system using the same inferior conventional systems (epoxy topcoat, polyurethane or latex).
3. Restore, enhance and extend the surface life of "new" or "oxidized" painted assets by 10 years using Nano coating.
4. Conventional paint systems including epoxies provide good corrosion resistance and initial surface hardness, but unfortunately fall short in long-term UV resistance and weathering. Two-component polyurethanes provide good UV resistance and weathering, but typically cost much more than epoxy or polyester topcoats. Conventional paint systems like topcoats and epoxies begin the oxidization process or "chalking" from weathering within 6 months from application. This surface chalking phenomenon is actually degraded paint that resides on the surface from UV exposure and weathering. The Nano coatings penetrate deep into the smallest pores within newly painted or highly oxidized paint surfaces to form a highly cross-link dense / hard coat surface. Aluwedo Nano coatings provide dramatically longer surface protection over conventional automotive, marine, aerospace and industrial paints including epoxies and polyurethanes.
Unique Advantages
1. Economic: with high-quality of paint, dust is difficult to form on the panel surface. It can be easily rushed away by little rain to realize self-cleaning. In this way, a lot of cleaning cost will be saved.
2. Environmentally friendly: the Nano aluminum composite panel is of super aging resistance, no coating change, no pollution, acid resistance, alkali resistance, and solvent resistance.
3. Highly durable: it is high durable, weather resistant, temperature resistant, and friction resistant
4. Recyclable: we recycle aluminum and polyethylene to reduce environment pollution.
Raw Material
a. High strength aluminum alloy A1100, A3003, A5052
b. LDPE core
c. Surface coating: PVDF coating, Kynar 500 (Paint supplier: Valspar, Nippon, PPG, Becker, etc.), and Dupont Adhesive film
Panel Specifications and Dimension
a. Thickness:3mm (0.12"), 4mm (0.16"), 5mm (0.2"), 6mm (0.24") Recommended thickness: 4mm(0.16")
b. Width: 850mm – 2000mm (34" – 80")
Recommended width: 1220mm (48.8"), 1250mm (50"), 1500mm (60"), 2000mm (80")
c. Length: as required
d. Aluminum thickness: 0.3mm (0.012") – 0.5mm (0.02")
e. *Custom width and length is available upon request (subject to the minimum order quantities)
Testing item | Standard | Result |
Unit weight | ASTM D792 | T 4mm=5.5kg/m2 |
Thermal expansion | ASTM D696 | 24-28 |
Thermal deformation temperature | ASTM D648 | 115 ℃ |
Thermal conduction | ASTM D976 | 0.102kcal/m.hr ℃ |
Flexural rigidity | ASTM D393 | 14.0*10^5 |
Impact resistance | ASTM D732 | 1.64kgf |
Adhesive strength | ASTM D903 | 0.77kg/mm |
Flexural elasticity | ASTM D790 | 4030kg/mm2 |
Shear resistance | ASTM D732 | 2.7kgf/mm2 |
Fire propagation | ASTM E84 | qualified |
Wind-pressure resistant | ASTM E330 | passed |
Waterproof property | ASTM E331 | passed |
Applicable Standards
1. American Architectural Manufacturers Association (AAMA) - AAMA 2605 Voluntary Specification
2. Performance Requirements and Test Procedures for Superior Performing Organic Coatings on Aluminum Extrusions and Panels
ASTM International
1. ASTM C297 Standard Test Method for Tensile Strength on Flat Sandwich Constructions in Flat Plane
2. ASTM C976 Standard Test Method for Thermal Performance of Building Assemblies by Means of a Calibrated Hot Box (Withdrawn 2002)
3. ASTM D635 Standard Test Method for Rate of Burning and/or Extent and Time of Burning of Self-Supporting Plastics in a Horizontal Position
4. ASTM D696 Standard Test Method for Coefficient of Linear Thermal Expansion of Plastics Between -30°C and 30°C With a Vitreous Silica Diameter.
5. ASTM D1037 Standard Test Method for Evaluating Properties of Wood-Base Fiber and Particle Panel Materials
6. ASTM D1781 Standard Test Method for Climbing Drum Peel for Adhesives
7. ASTM D1929 Standard Test Method for Determining Ignition Temperature of Plastics
8. ASTM E8 Standard Test Method for Tension Testing of Metallic Materials
9. ASTM E72 Standard Test Methods for Conducting Strength Tests of Panels for Building Construction
10. ASTM E84 Standard Test Method for Surface Burning Characteristics of Building Materials
11. ASTM E108 (Modified) Standard Test Methods for Fire Tests of Roof Coverings
12. ASTM E283 Standard Test Method for Determining the Rate of Air Leakage Through Exterior Windows, Curtain Walls, and Doors Under Specified Pressure Difference Across the Specimen
13. ASTM E330 Standard Test Method for Structural Performance of Exterior Windows, Curtain Walls, and Doors by Uniform Static Air Pressure Difference
14. ASTM E331 Standard Test Method for Water Penetration of Exterior Windows, Curtain Walls, and Doors by Uniform Static Air Pressure Difference
15. ASTM E413 Standard Classification for Rating Sound Insulation
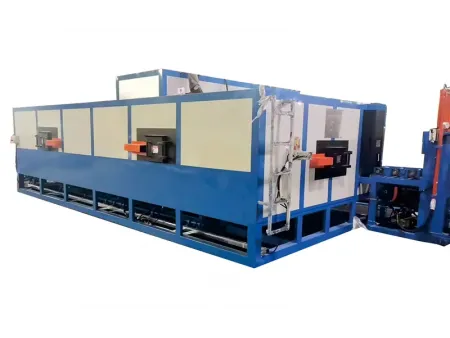